Injection molds using the hot runner molding process have significant advantages, which are mainly reflected in material conservation, efficiency improvement, quality optimization and production flexibility, etc. The following is a specific analysis:
I. Material Conservation
1. Waste without cold flow channels
In traditional cold runner injection molding, the plastic inside the runner cools and solidifies to form waste, which requires additional treatment or recycling.
3. The hot runner keeps the plastic inside the runner molten through continuous heating, generating no waste and achieving a material utilization rate close to 100%.
4. Case: When manufacturing automotive bumpers, hot runners can save 15% to 20% of raw material costs.
5. Reduce material waste
6. There is no need to reserve space for the cold runner, and the mold design is more compact, which can reduce the material usage.
Ii. Efficiency Improvement
1. Shorten the molding cycle
2. Cold runners need to wait for the runner to cool down before mold opening, while hot runners can be directly injection molded, reducing the mold opening time by 30% to 50%.
3. Data: The forming cycle of thin-walled parts can be shortened from 10 seconds to 5 seconds.
4. Automated Production
5. There is no need for manual trimming of the gate, and it can directly proceed to the next process, making it suitable for large-scale automated production.
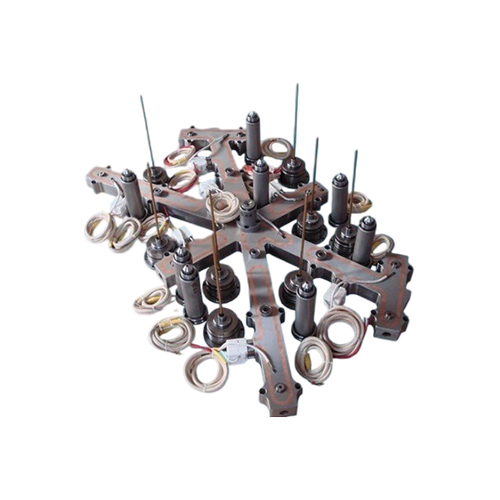
Iii. Quality Optimization
1. Higher quality of plastic parts
2. No gate marks on the surface: The needle valve type hot runner can achieve seamless injection molding, enhancing the aesthetic appeal of the product.
3. High dimensional accuracy: The flow channel temperature is uniform, reducing shrinkage and deformation, and the dimensional stability is improved by 20%-30%.
4. Good mechanical properties: Without cold material filling, the internal stress of the plastic part is small, and the impact resistance is enhanced.
5. Strong process stability
6. The temperature control of the hot runner system is precise, reducing the defective rate caused by temperature fluctuations.
Iv. Production Flexibility
1. Multi-gate design
2. Support multi-point injection of complex molds to solve the flow problems of large plastic parts or thin-walled parts.
3. Case: When manufacturing automotive instrument panels, hot runners can achieve uniform glue injection across multiple gates, avoiding short shots and weld marks.
4. Material Compatibility
5. It is applicable to a variety of plastic materials, including high-temperature engineering plastics (such as PEEK) and heat-sensitive materials (such as PVC).
V. Other Advantages
1. Environmental benefits
2. Reducing waste generation and lowering recycling costs is in line with the trend of green manufacturing.
3. Economic Benefits
In the long term, material savings and efficiency improvements can significantly reduce production costs.
Vi. Limitations and Coping Strategies
Despite its obvious advantages, hot runners also face the following challenges:
1. High initial investment: The mold cost is 30%-50% higher than that of the cold runner.
2. Response: Quickly recover costs through material savings and efficiency improvements.
3. High technical requirements: Professional personnel are needed to maintain the temperature control system to prevent temperature loss of control.
4. Response: Select experienced suppliers and provide regular training for operators.